
About
âTemperature monitoring and accurate drying end time determination are crucial for final product quality in vacuum freeze-drying of pharmaceuticals. Additionally, non-invasive temperature monitoring tools coupled with fast ice crystal size prediction models can be used to optimize the drying stage and product quality. The current monitoring tools, such as thermocouples and Pirani gauge pressure sensors, have several limitations such as affecting product dynamics or imprecise endpoint determination.
In this research project, the applications of an infrared (IR) thermography sensor applied to freeze-drying processes are studied. The current prototype is specially designed to be placed inside the drying chamber with minimal impact on batch dynamics. This sensor allows the monitoring of the whole axial temperature of the product in the vials and the application of multivariate image analysis since it yields high-quality thermal data on the process.
IR thermography is a promising tool for monitoring freeze-drying processes and future sensor models will be smaller to allow even more practical applications.


Publications
1. Harguindeguy M, Fissore D. Micro Freeze-Dryer and Infrared-Based PATâŻ: Novel Tools for Primary Drying Design Space Determination of Freeze-Drying Processes. Pharm Reserach. 2021;38:707-719. doi:10.1007/s11095-021-03021-x
2. Harguindeguy M, Fissore D. Temperature/end point monitoring and modelling of a batch freeze-drying process using an infrared camera. Eur J Pharm Biopharm. 2021;158(January):113-122. doi:10.1016/j.ejpb.2020.10.023
3. Bobba S, Harguindeguy M, Colucci D, Fissore D. Diffuse interface model of the freeze-drying process of individually frozen products. Dry Technol. 2020;38(5-6):758-774. doi:10.1080/07373937.2019.1710711
4. Colucci D, Fissore D, Barresi AA, Braatz RD. A new mathematical model for monitoring the temporal evolution of the ice crystal size distribution during freezing in pharmaceutical solutions. Eur J Pharm Biopharm. 2020;148(January):148-159. doi:10.1016/j.ejpb.2020.01.004
5. Colucci D, Morra L, Zhang X, Fissore D, Lamberti F. An automatic computer vision pipeline for the in-line monitoring of freeze-drying processes. Comput Ind. 2020;115:103184. doi:10.1016/j.compind.2019.103184
6. Harguindeguy M, Bobba S, Colucci D, Fissore D. Effect of vacuum freeze-drying on the antioxidant properties of eggplants (Solanum melongena L.). Dry Technol. 2020;39(January):3-18. doi:10.1080/07373937.2019.1699834
7. Colucci D, Maniaci R, Fissore D. Monitoring of the freezing stage in a freeze-drying process using IR thermography. Int J Pharm. 2019;566(May):488-499. doi:10.1016/j.ijpharm.2019.06.005
8. Colucci D, Prats-MontalbĂĄn JM, Fissore D, Ferrer A. Application of multivariate image analysis for on-line monitoring of a freeze-drying process for pharmaceutical products in vials. Chemom Intell Lab Syst. 2019;187(February):19-27. doi:10.1016/j.chemolab.2019.02.004
9. Colucci D, Prats-MontalbĂĄn JM, Ferrer A, Fissore D. Infrared Imaging and Multivariate Image Analysis (MIA). In: Freeze Drying of Pharmaceutical Products. ; 2019:53-76. doi:10.1201/9780429022074-4
10. Colucci D, Prats-MontalbĂĄn JM, Ferrer A, Fissore D. On-line product quality and process failure monitoring in freeze-drying of pharmaceutical products. Dry Technol. 2019;39(2):134-147. doi:10.1080/07373937.2019.1614949
11. Lietta E, Colucci D, Distefano G, Fissore D. On the use of infrared thermography for monitoring a vial freeze-drying process. J Pharm Sci. 2018;108(1):391-398. doi:10.1016/j.xphs.2018.07.025
Thank you for your interest in infrared monitoring of freeze-drying processes.
For more information contact Dr. Davide Fissore.
Full Professor - Politecnico di Torino
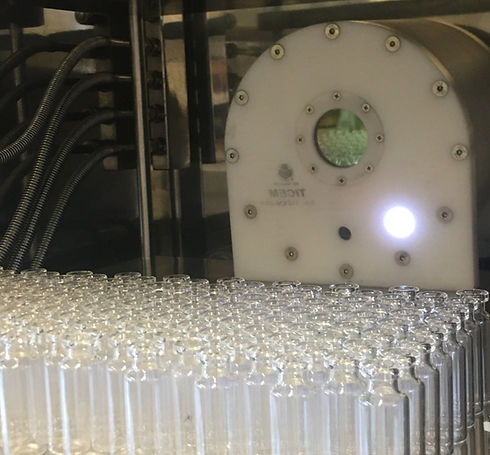